Refuge chambers are a significant but much-needed investment. With the growth of safety requirements, refuge chambers have become commonplace for the safe retreat of personnel engaged in tunnelling and underground construction. But, as these are finite projects, what happens to a refuge alternative upon completion?
Extending the life of refuge chambers through remanufacturing and upgrades is both safe and cost-effective. The process generates added value; however, adhering to proper specifications is crucial to ensure high safety standards remain. Recently, the global tunnelling company Herrenknecht remanufactured and extended several TunnelSAFE chambers to use in new endeavours.
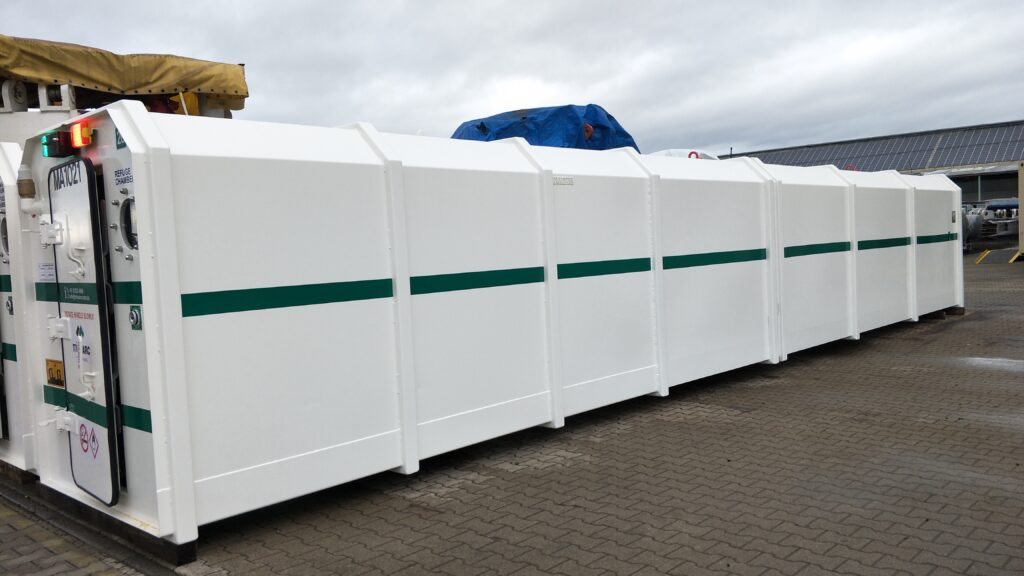
Remanufacturing a Refuge Chamber for Tunnelling
The remanufacturing process applies to any used tunnelling refuge chamber. The method involves transforming a used chamber into a newer, fit for purpose model. Ensuring it meets the organisation’s safety standards is a significant consideration, as are government guidelines and MineARC Systems quality assurance.
Initially, used shelters are returned from the site to be assessed and stripped. Allowing the full extent of restoration and updates required to bring the chamber back to a high safety standard to be determined.
For this project, Herrenknecht collaborated with MineARC Systems to determine the appropriate upgrades and parts required for the individual chamber. Once a chamber is cleaned, blasted, and freshly painted the next stage is to install all the new components, followed by final inspection and sign-off.
A unique addition to the Herrenknecht project was the chamber extension. Due to various safety regulations across different countries, several chambers required an extension to comply with new safety standards. MineARC Australia’s team of engineers collaborated with the Rebuild Services in Germany to complete the project. The extension model was fabricated on-site in Perth and shipped to Germany and additional spare parts.
Commissioning and CE Certification
A qualified MineARC team member performs the project’s final stage, commissioning and CE certification. A quality-focused process ensures the refuge chamber meets the government, site’s, and MineARC’s safety requirements.
Commissioning brings the safe refuge into working condition, following delivery and installation. Then, checking that all components and systems are installed, tested, operated, and maintained according to the operational requirements.
Ensuring remanufactured chambers can be safely used in a hazardous situation is a priority.
Rigorous inspections and tests occur at all stages. Technical standards are set out to ensure the safety of personnel and the integrity of the equipment.
Remanufacturing guarantees that the refuge alternative adheres to safety guidelines and is fitted with the latest safety technology, extending the investment beyond a project’s lifetime.